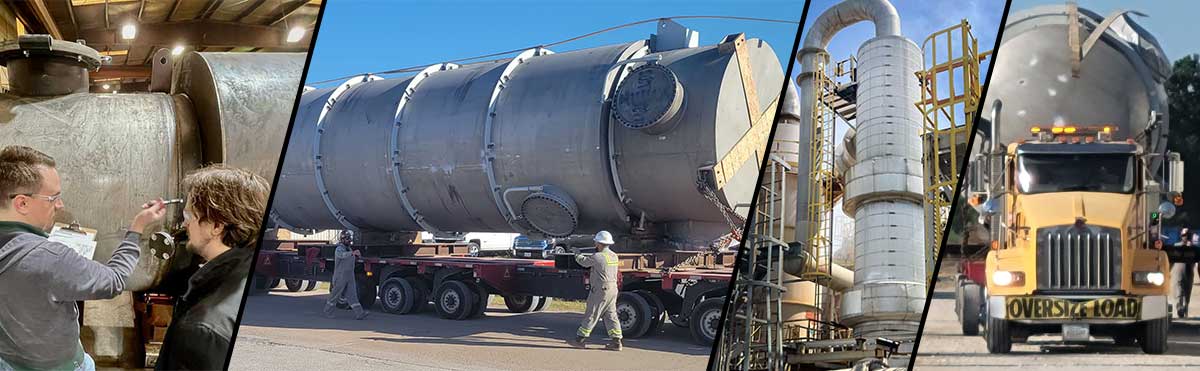

High-Temperature Engineered Solutions
Temperature and Flow Mapping to Eliminate Thermal Stress and Corrosion for Improved Plant Reliability
Challenge accepted! Unique customers and process streams require High-Temperature Engineered Solutions, with an emphasis on custom-tailored designs. Utilizing temperature and flow mapping, our engineering team develops a digital twin of the ideal unit for every individual stream to allow for accurate, true-to-life modeling. The result is industry-leading design solutions to eliminate thermal stress and corrosion common in these environments, offering improved reliability.
The CG Thermal Experience:
- High-temperature design expertise
- Unique design for your unique reliability challenge
- Adaptable solutions for high-temperature
- Responsiveness and agility
- Transparency of results
- Customer input to ensure success
We want to see your plant succeed!
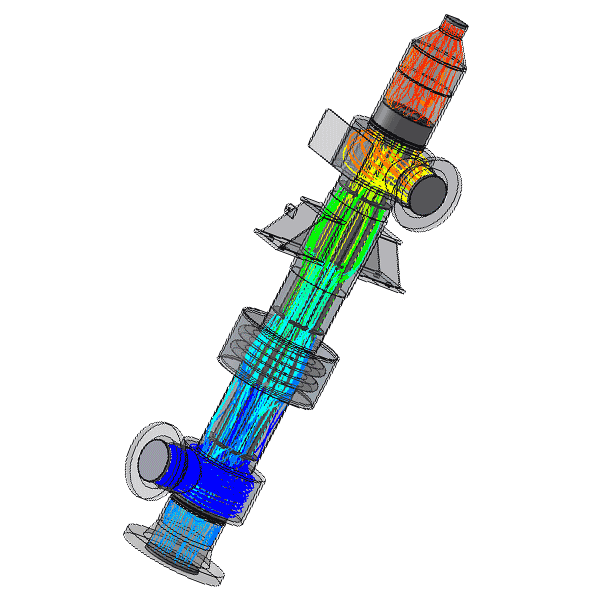
Consulting & Engineering Services for High-Temperature
With a hands-on approach and customer-focused discovery process, our engineers develop a plan to mitigate inefficiencies and improve plant reliability. Engineering analysis results are provided with or without a fabrication contract – we want to see your plant succeed!
What to expect:
- Site audit
- Engineering analysis and design
- CFD / FEA / ASME B31.3 analysis where applicable
- Duct strain analysis
- Fabrication and installation drawings provided
- Execution consulting available
- Materials and supplies recommendation
- Fabrication, controls and instruments, fan packages
AirBTU VPRR High-Temperature Gas Recuperator
By integrating an AirBTU VPRR heat transfer solution, industry professionals can avoid common pitfalls and “design in” reliability and efficiency.
AirBTU VPRR features:
- Tube wall temperature mapping
- Eliminates stress failures
- Reduces pressure drops
- Maximizes thermal efficiency
- Minimizes maintenance downtime
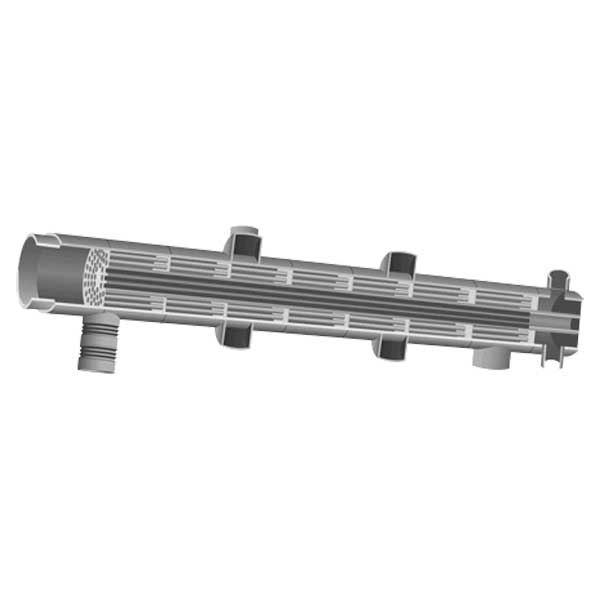
AirBTU HTXP High-Temperature and High-Pressure Exchanger
Using an innovative design including a novel application of high performance insulation the AirBTU HTXP allows for thermal expansion, without the material stresses typical in high-temperature and high-pressure process streams.
AirBTU HTXP features:
- Allows for thermal expansion without causing material stress
- Supports both high temperature and high pressure streams
- Eliminates hot spots and maintains suitable material temperatures
- Easy disassembly for repair and cleaning
- Optimal design allows for lower CAPEX
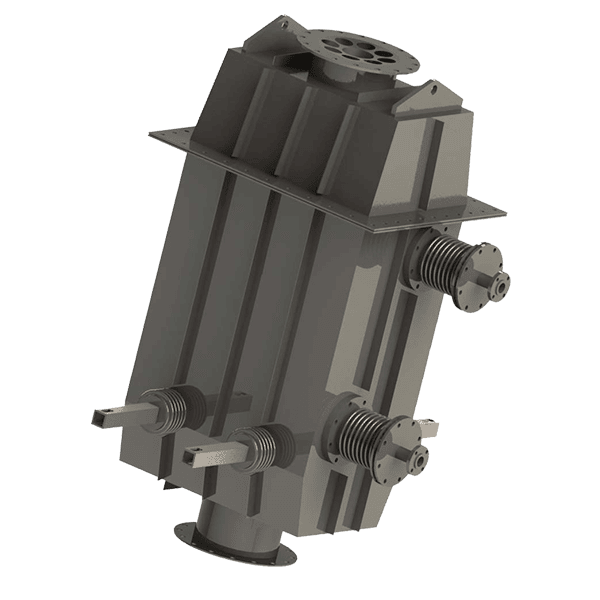
Quench Lid Advanced – Innovation for Quench Acid Gas / Adiabatic Coolers
Along with innovative design techniques, our high-temperature engineering team utilizes specialty materials to solve our customers’ unique problems. Our ground-breaking United States Patent-Pending Quench Lid Advanced offers a corrosion-resistant hot gas nozzle and lid for an adiabatic gas cooler, greatly reducing the inherent corrosion of quench gas coolers. This next-generation design greatly improves the reliability of quench gas coolers in harsh and corrosive environments for which even specialty metals do not offer long-term reliability.
In the case of quench gas coolers, adiabatic coolers, and hot gas scrubbers used in sulfuric acid regeneration plants, corrosion is an inherent and universal issue in the system. SO2 and SO3 gas typically enter the scrubber vessel from a decomposition furnace. As this hot gas enters, ambient temperature water is released from the lid above cooling the acid to near ambient. Typically, corrosion is imminent during this cooling process, as acid gas forms in the cooled stream.
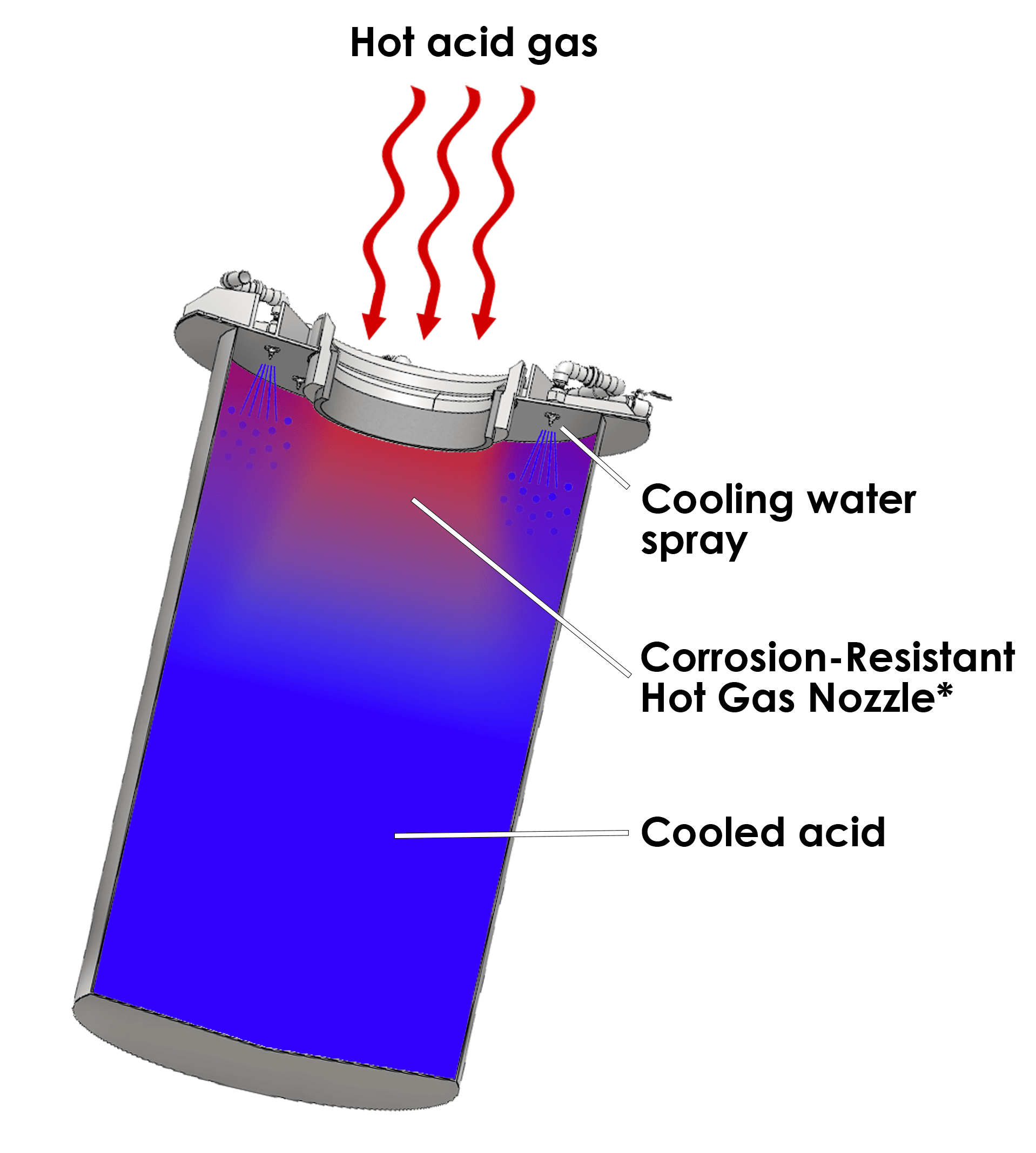
Utilizing the Quench Lid Advanced eliminates corrosion on the gas nozzles, and in turn, significantly limits the area of corrosion. This greatly extends the life of the unit and prevents the premature failure inherent in these systems. This proven design can be used to manufacture new units or replacement scrubber lids can be retrofitted to existing ones, including designs utilizing wet-walled towers. The benefits of reduced downtime and increased production will result in lower OPEX and overall improved throughput of your plant.
Contact CG Thermal today, and let our engineering experts solve your unique design challenges. We’re here to help!
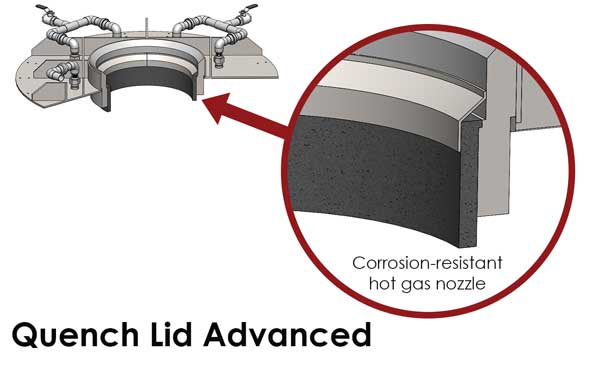