The Premier Soil, Air and Water Remediation Conference
We hope to see you at Florida Remediation Conference 2024, the premier soil, air and water remediation conferences in the industry! Our team of engineers is eager to discuss your remediation needs, and help tackle your challenges involving harsh and corrosive process streams. Whether you require a fully designed turnkey or modular system ski, consulting, or plant layout and design CG Thermal’s systems group is ready to provide assistance.
“The Florida Remediation Conference (FRC) is one of the premier soil, air and water remediation conferences in the industry. FRC attracts over 400 attendees comprised of a mix of industry representatives, developers, consultants and contractors, and over 70 exhibitors and sponsors from across the country. It is far from just being a Florida event.
If you are in the remediation and redevelopment sectors, you need to attend FRC 2024.”
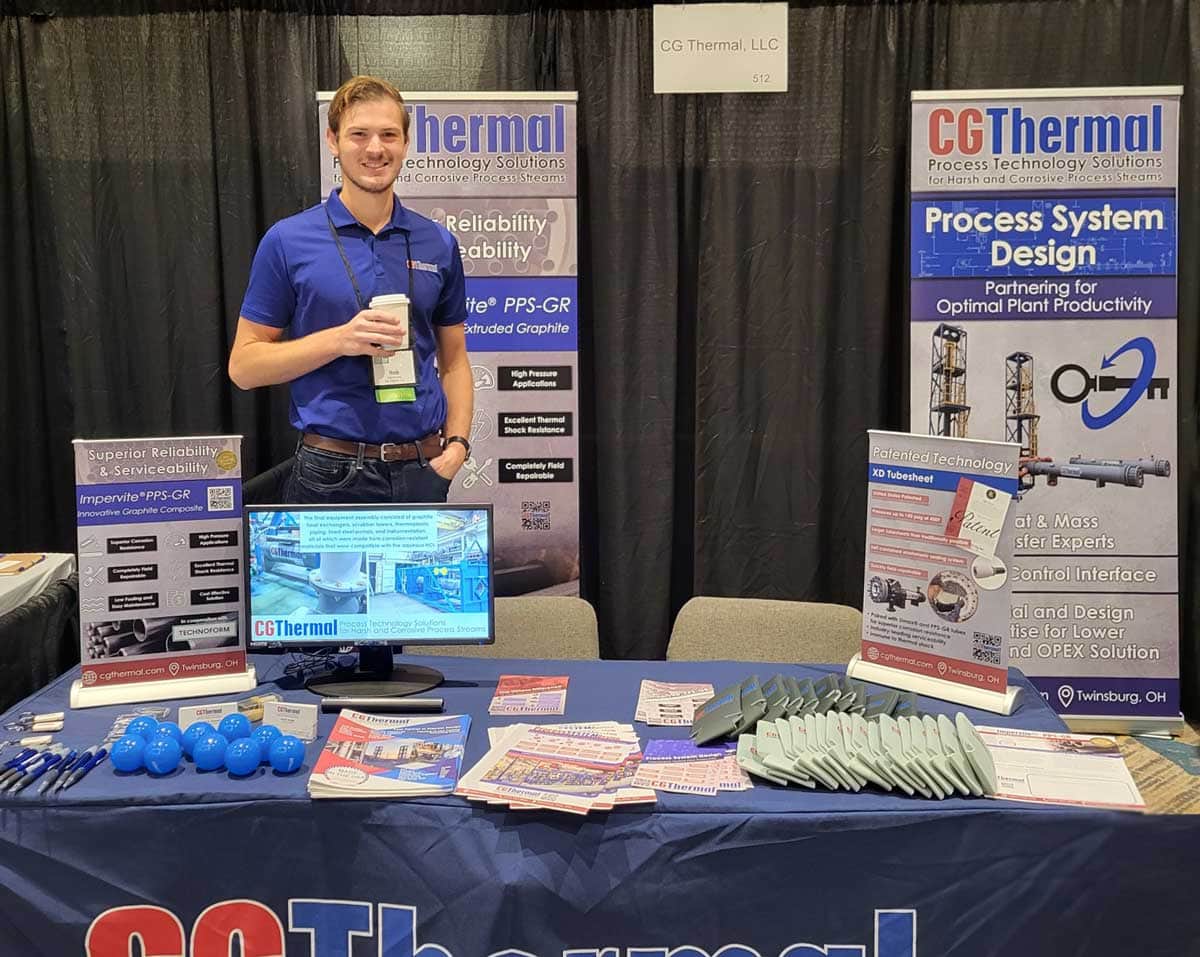
Schedule a meeting:
Our engineering team will be on-site and ready to discuss practical and innovative solutions to your engineering problems.
Click here to schedule your in-person consultation with one of our process industry experts.
Innovative Materials and Solutions for Harsh & Corrosive Process Streams
At CG Thermal we are decidedly customer-focused, and approach each new project with a desire to achieve our customer’s goals and process requirements in the most efficient and cost-effective manner. We have particular expertise in corrosive and high temperature process streams, and provide a range of services from individual equipment to full turnkey systems to engineering design and plant layout consulting.
Let’s discuss your harsh and corrosive process stream today!
Process System Design
We combine our extensive heat/mass transfer knowledge and fabrication capabilities with design and process expertise. The result is optimal, proven processing technology while incurring the lowest possible capital and operating expenses (CAPEX/OPEX) for the customer. Ultimately, team understands that the engineering specifications for industrial process equipment are as different as the customers themselves. We are dedicated to working within your framework to provide the custom services that your job requires. To that end, we offer four options to address these needs:
Turnkey Packaged System — Custom designed skid package system may include instrumentation, PLC, HMI, piping, electric and platforms, ladders, and other safety features per job requirements
- Consulting Services — Trouble-shooting, optimizing, and evaluating of existing plant operations
- Engineering Design Package — Complete engineering and operations design and documentation including Haz-Op review on customer site, and controls and control instrument loops
- Major Equipment Package — Exchangers, vessels, pumps, filters, controls, drums, tanks, etc.
Impervite® Advanced Graphite: An Advance in Non-Metallic Materials
The Impervite® Advanced Graphite Heat Exchanger design incorporates proven tube to tubesheet seal and the field-repairability of our Umax SiC Ceramic Heat Exchanger with the quality that the industry has long associated with Impervite®. Additionally, the Impervite® Advanced Graphite tubes can be used in conjunction with our United States Patented XD tubesheet, capable of pressures up to 150 psig at 400F.
Recently, the Impervite® Advanced Graphite design received the prestigious 2023 VAALER Award for Innovation in the Chemical Industry. Click here to learn more about Impervite® Advanced Graphite and the award.
AirBTU VPRR: High Temperature Energy Capture
Are you looking to improve the reliability of your high-temperature heat transfer equipment? Are you looking for technology that will allow you to reutilize waste heat at higher temperatures? If so, you need to visit us in Pasadena. By integrating our AirBTU VPRR heat transfer solution, industry professionals can avoid common pitfalls and “design in” reliability and efficiency. The AirBTU VPRR is designed to:
- Avoid cold-end corrosion. The introduction of low-temperature air can result in cold spots within a recuperator, causing condensation of some constituents of the process gas stream. The resulting reaction between this corrosive condensate and the heat exchanger surface is commonly referred to as cold-end corrosion. This destructive mechanism is “designed out” of the AirBTU VPRR, making it the ideal Heat Exchanger for Sulfuric Acid Applications.
- Eliminate stress failures. Temperature gradients across the tube bundle can lead to uneven stress concentrations at the tube-to-tube-sheet connections. These result in tubesheet failures with subsequent losses in production and costly repairs. We design in uniformity to eliminate this failure mode.
- Reduce pressure drops. Our VPRR features a proprietary design that reduces pressure drops for the best energy efficiency.
- Maximize thermal efficiency. Flow dynamics modeling is used to evaluate tube layouts and pass arrangements to create a symmetric design with optimal film coefficients and overall heat transfer rate. The resulting design requires less surface area and minimizes material and fabrication costs.
- Minimize maintenance downtime. In addition to minimizing failures caused by cold end corrosion and uneven mechanical stresses, we can “design-out” the potential for fouling.