Plan Your Visit & Learn About our Patented Technology
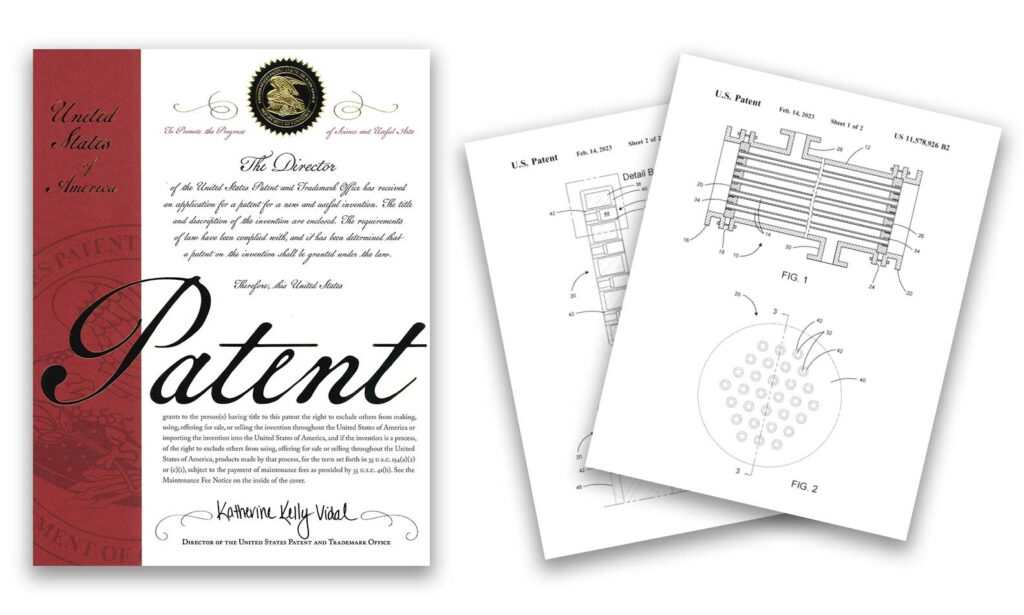
CG Thermal awarded a United States Patent on the revolutionary XD tubesheet
Visit CG Thermal for innovation and insight in heat transfer at Heat Exchanger World Americas 2023. Our team of experts will be there along with industry partners, Technoform, to discuss process technology solutions for harsh and corrosive process streams. Additionally, we will be showcasing our newly patented XD Tubesheet design. Capable of pressures up to 150 psig at 400F and able to be used in larger tubesheet designs, it features a self-contained elastomeric sealing system for quick and easy tube maintenance. With the option for customers to use either Umax® Advanced Ceramic or Impervite® PPS-GR tubes, the XD Tubesheet pushes the boundaries of what’s possible for addressing corrosive environments in heat transfer technology.
At CG Thermal we work tirelessly to bring innovation and new technologies to heat transfer in harsh and corrosive process streams. At Heat Exchanger World Americas we hope to meet with your team and discuss your process streams and how we can help!
Click here to schedule your in-person consultation with one of our process industry experts.
4th Annual Heat Exchanger World Americas
“…During the exhibition, manufacturers, suppliers and distributors will have the chance to showcase their latest products, technologies, services and capabilities, while simultaneously forming new business relationships and reaffirming old ones. The technical conference will feature heat exchanger experts from various sectors, who will focus on a wide range of topics related to the heat exchanger and heat transfer industries…”
– Heat Exchanger World
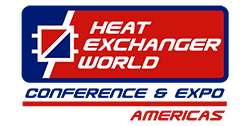
Heat Exchanger World Americas 2023 will take place from October 17-18th at the Pasadena Convention Center in Pasadena, TX. You don’t want to miss it!
Want to see CG Thermal’s exhibit? Register for Heat Exchanger World Americas now by clicking here!
Don’t wait for the show, contact us today for all your harsh and corrosive processing needs.
Impervite® PPS-GR Heat Exchanger
INNOVATIVE TECHNOLOGY IMPROVING RELIABILITY AND SERVICEABILITY
The revolutionary technology of Impervite® PPS-GR features a novel composite graphite tube made available in partnership with Technoform. The material offers the corrosion resistance expected from traditional impregnated graphite, as well as a unique tube to tube sheet sealing system resulting in ease of maintenance, high reliability, and minimal downtime. Below are just some of the many benefits of Impervite® PPS-GR.
- Low Fouling and Ease of Maintenance
- Completely Field Repairable
- Proprietary Self-Contained Elastomeric Sealing System
- Superior Thermal and Mechanical Shock Resistance
Are you looking for less downtime and lower maintenance costs associated with your heat exchangers? Click here to learn about what CG Thermal has to offer.
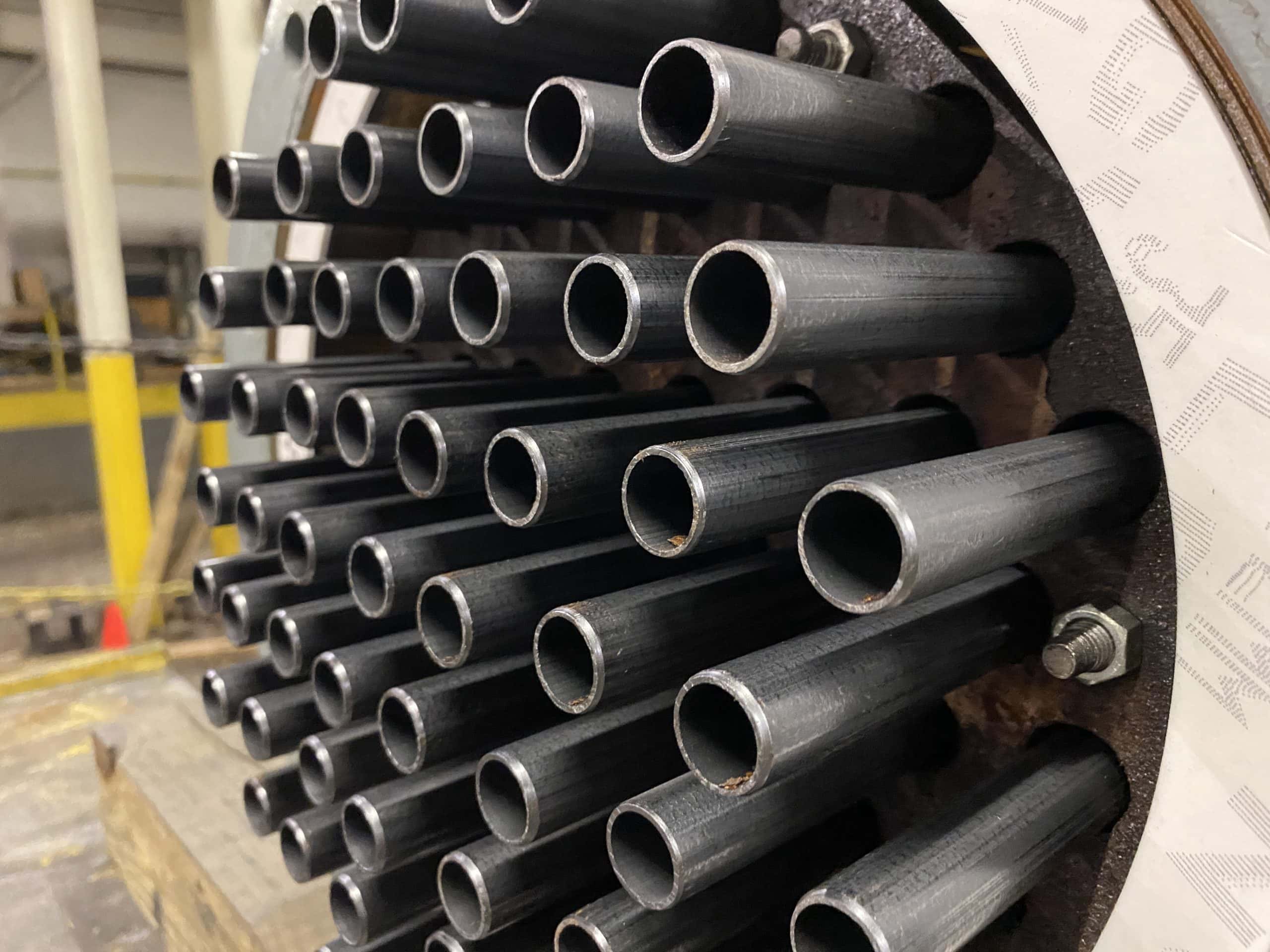
AirBTU VPRR: High Temperature Energy Capture
Are you looking to improve the reliability of your high-temperature heat transfer equipment? Are you looking for technology that will allow you to reutilize waste heat at higher temperatures? If so, you need to visit us in Pasadena. By integrating our AirBTU VPRR heat transfer solution, industry professionals can avoid common pitfalls and “design in” reliability and efficiency. The AirBTU VPRR is designed to:
- Avoid cold-end corrosion. The introduction of low-temperature air can result in cold spots within a recuperator, causing condensation of some constituents of the process gas stream. The resulting reaction between this corrosive condensate and the heat exchanger surface is commonly referred to as cold-end corrosion. This destructive mechanism is “designed out” of the AirBTU VPRR, making it the ideal Heat Exchanger for Sulfuric Acid Applications.
- Eliminate stress failures. Temperature gradients across the tube bundle can lead to uneven stress concentrations at the tube-to-tube-sheet connections. These result in tubesheet failures with subsequent losses in production and costly repairs. We design in uniformity to eliminate this failure mode.
- Reduce pressure drops. Our VPRR features a proprietary design that reduces pressure drops for the best energy efficiency.
- Maximize thermal efficiency. Flow dynamics modeling is used to evaluate tube layouts and pass arrangements to create a symmetric design with optimal film coefficients and overall heat transfer rate. The resulting design requires less surface area and minimizes material and fabrication costs.
- Minimize maintenance downtime. In addition to minimizing failures caused by cold end corrosion and uneven mechanical stresses, we can “design-out” the potential for fouling.
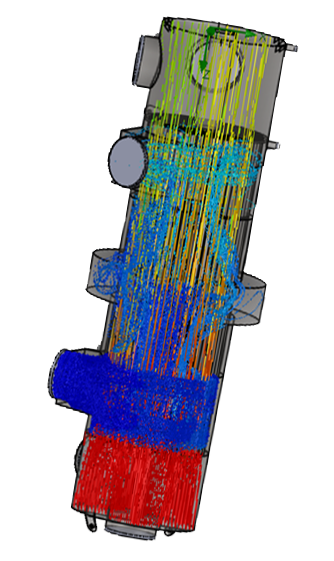