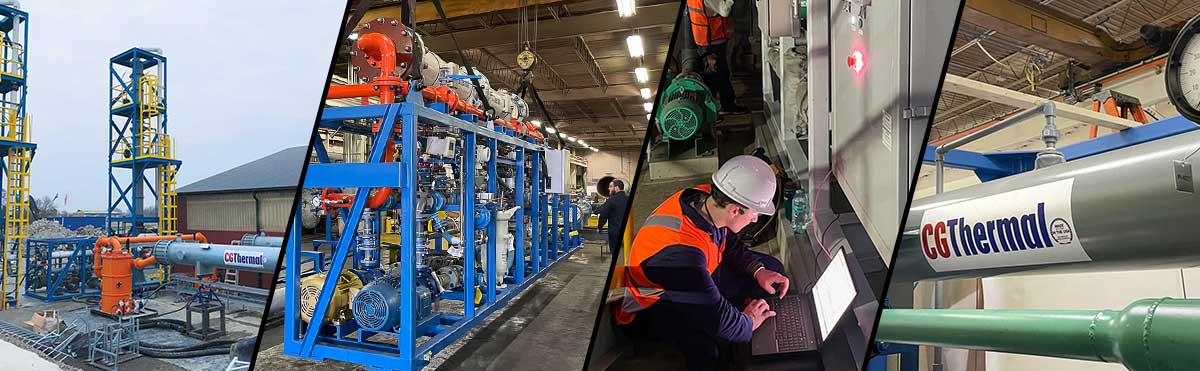

Process and System Design
Chemical Process System Design, Turnkey and Modular Systems, Consulting, Engineering Design, and Major Equipment
CG Thermal is a leading manufacturer of chemical process systems, including heat exchangers, absorbers, and other OEM process equipment. With proven expertise in thermal modeling, material selection, installation, and maintenance, we combine advanced heat and mass transfer knowledge with strong mechanical and process design capabilities to deliver efficient, reliable systems that minimize CAPEX and OPEX.
Our team works closely with customers and industry experts to develop optimal solutions—whether for pilot plants, modular systems, or full-scale process equipment. From emerging market prototypes to turnkey packaged systems, we tailor each project to meet unique engineering specifications, ensuring long service life, enhanced corrosion resistance, and maximum plant productivity.
We collaborate with technology partners to recommend the most appropriate materials for your process conditions, including standard and special metal alloys, advanced corrosion-resistant options, and custom configurations. Transparency, open communication, and a commitment to continuous improvement drive innovation across all our products and services.
Our Capabilities Include:
Turnkey Packaged & Modular Plant Systems – Custom skid packages with instrumentation, PLC/HMI, piping, electrical, platforms, ladders, and safety features.
Consulting Services – Troubleshooting, optimization, and performance evaluation of existing operations.
Engineering Design Packages – Complete engineering, operations documentation, on-site Haz-Op reviews, controls, and instrument loop design.
Major Equipment Packages – Heat exchangers, vessels, pumps, filters, controls, drums, tanks, and more.
Partner with CG Thermal for proven chemical process solutions that deliver efficiency, reliability, and competitive advantage!
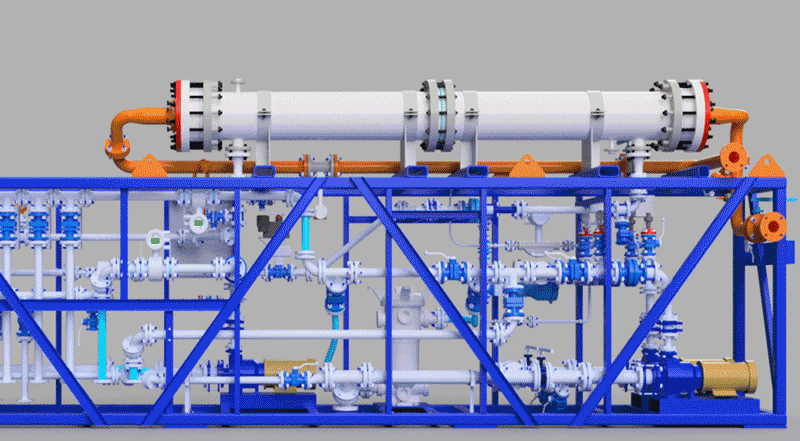
Let us help your plant succeed!
Our Systems & Services
Sulfuric Acid Systems
Engineered sulfuric acid solutions for dilution, concentration, regeneration, and efficient, safe handling.
Hydrochloric Acid
Corrosion-resistant hydrochloric acid (HCl) systems designed for safety, reliability, and long service life.
Nitric Acid Systems
Precision temperature control for titanium pickling and chem-milling using Umax® ceramic heat exchangers.
Control Panels & Automation
PLC/HMI control panels and automation services optimized for complex process operations.
Areas of Expertise
CG Thermal has extensive experience with chemical process system design and heat and mass transfer with particular focus on aggressive acids such as hydrochloric acid, sulfuric acid, hydrofluoric acid, phosphoric acid, nitric acid, and bromine. Our team of experts will assist you in designing the optimum solution for the application at hand.
- Dilution
- Synthesis
- Scrubbers
- Absorption
- Desorption
- Recovery
- Azeotrope breaking
- Temperature control
- Defluorination
Properly designed dilution systems work to address exothermic reactions and control product quality in industries like chemical processing, steel, refining, battery manufacturing, and more. CG Thermal manufactures skid-mounted, sulfuric acid dilution systems that can be custom-designed to address a variety of process requirements. We use Umax Advanced Ceramic or Impervite ® impervious graphite heat exchangers for their outstanding resistance to corrosion and thermal efficiency.
Responsible for combustion, cooling of gas, absorption, and solution cooling, the synthesis process works to extract and optimize the ideal properties from reaction products. Synthesis minimizes environmental impacts and improves production safety and efficiency. At CG Thermal, we offer a unique burner design that results in an optimal CAPEX/OPEX solution.
Scrubbers control air pollution by removing particulate matter or gases from the air in chemical processing, steel production, and other industries. CG Thermal offers a variety of solutions and process system approaches to accomplish this, including sour gas stripping, stream conditioning, and VOC stream stripping.
The absorption process increases acid concentrations for feedstock, either isothermally or adiabatically. The absorption method impacts the maximum concentration of acid that can be maintained in a liquid, as well as the temperature at which the process can be carried out.
Thermal desorption systems use heat to increase contaminant volatility — often AHCL in gas or liquid form — so that it can be removed from production for reuse or disposal.
Acid waste is one of the most hazardous manufacturing byproducts — and also among the most expensive in terms of disposal. Recovery and reuse of these chemicals can reduce operating costs and improve environmental sustainability. With a complete line of fluoropolymer-lined components, our vacuum recovery systems concentrate H2S04 using a single- or multiple-effect arrangement.
A required process when producing AHCL from HCL, azeotrope breaking (distillation) involves adding components to create a heterogeneous lower-boiling azeotrope. At CG Thermal, we can design vacuum-pressure or positive-pressure azeotrope breaking systems.
Temperature control is vital in chemical milling, pickling, and other applications in which thermal precision is necessary to maintain product quality. Our team can produce a complete nitric acid skid-mounted system that includes the essential components — pumping, piping, and controls — to accurately moderate temperature and maximize production.
Our team of experts provides defluorination process design and technology for the removal of HF from purified acid streams and hydrometallurgy, as well as manufacturing and design of DF columns.
Prototypes & Pilot Plants
Turn your prototype concepts and pilot plant designs into proven, operational systems with CG Thermal’s engineering expertise.
Our team combines advanced heat and mass transfer knowledge with high-temperature process design experience to deliver innovative, reliable solutions for your most challenging applications. With chemical, mechanical, and controls engineers working in unison, we provide cost-effective, custom-engineered systems tailored to your exact process requirements.
From emerging market applications to established industrial processes, our pilot plant equipment and prototype systems are built using time-tested heat exchanger technology, optimized piping designs, and materials proven for corrosion resistance and high-temperature reliability. Whether you need a one-off prototype or a scalable pilot plant ready for full production, CG Thermal delivers results that minimize risk and maximize performance.
Technical Documents & Resources
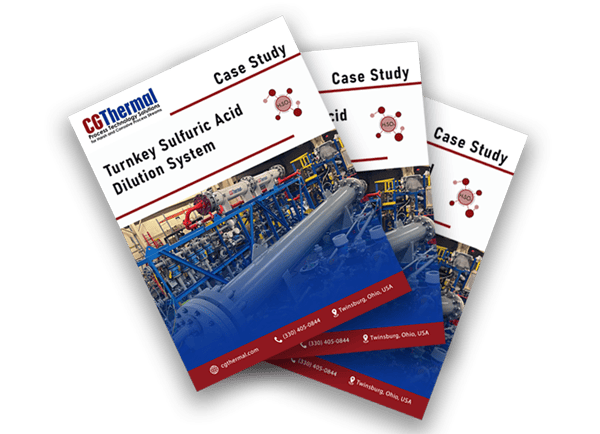
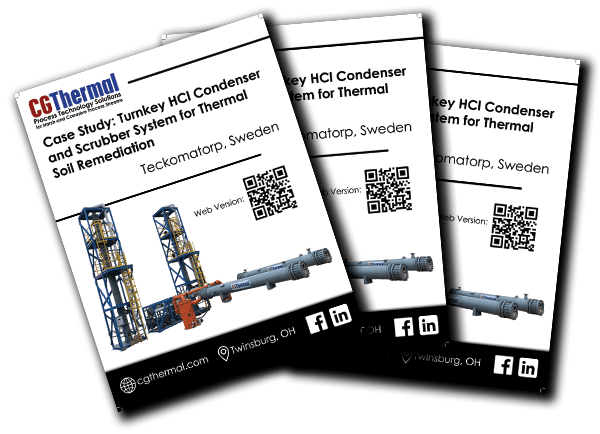