Sulfuric Acid Systems
Your Experts in H2SO4 Dilution, Dewatering, and Regeneration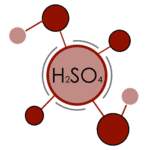
Sulfuric Acid Systems
CG Thermal provides expertise in developing sulfuric acid systems for processing Sulfuric acid (H2S04). Sulfuric acid is the most commonly produced and highly critical industrial chemical worldwide, useful in producing hundreds of other essential compounds.
Moreover, production of many important acids relies chiefly on sulfuric acid, and it is also used as a catalyst in the alkylation process of high-octane gasoline production in petroleum refining. In addition to being a good catalyst, it is highly reactive with water, and therefore commonly used in dehydration processes.
Industries & Uses
- Production of phosphoric acid
- Fertilizer production
- Production of esters
- Nitration of toluene and aromatics
- Dehydration processes
- Metal manufacturing, including copper and zinc
- Cleaning of steel
Its popularity and utility continue to soar worldwide, growing over 3% a year, partly fueled by growing demand in the Asia-Pacific region. Because sulfuric acid is used in manufacturing important products such as phones, electronics, paper, specialty chemicals, personal care products, and fertilizer, it increasingly influences economies worldwide. As heat and mass transfer experts, the CG Thermal systems group has been instrumental in implementing sulfuric acid systems used in this popular and growing industry.
Dilution
A properly designed dilution system, with attention to materials of construction and control, is critical to obtaining the desired end result. First, the concentrated acid is introduced to the feed water in a mixing tee. As a result, substantial heat is generated in the process, therefore the ratios and rate of dilution must be carefully controlled and monitored.
CG Thermal is your partner in the process design. We provide skid mounted sulfuric acid dilution systems custom designed for your process requirements. If you are not looking for a skid mounted system, we can provide a menu of engineering services to sync with your in house capabilities, or simply the components per your specifications. Click here to learn more about our Process System Design services.
Although our Impervite graphite excels in harsh and corrosive process streams up to certain concentrations and temperature ratings, our Umax Advanced Ceramic heat exchangers are universally corrosion and erosion resistant, making them the optimal choice for sulfuric acid dilution systems. The Umax tube will not corrode at any concentration and boasts a lifetime guarantee. Since it is 50% harder than tungsten carbide, the Umax tube can be used at higher velocities without concern of erosion. The ability to operate at higher velocities coupled with it’s high thermal conductivity, make it the most thermally efficient choice. Ultimately, the innovative tubesheet design offers superior serviceability, allowing for easy access to all tubes for cleaning and in-house repair.
We Can Help
We will include a recirculating loop to ensure thorough mixing and reduce the temperature seen by system components. If your plant would benefit from redundancy, we will design with (2) heat exchangers in series.
The system can be supplied with completely customized instrument and controls for receiving temperature, flow, pressure, and concentration inputs and generating outputs to control valves and pumps to maintain the desired outlet temperature and concentration. An HDMI can either be skid or remotely mounted. We can terminate at the PLC compatible with your Digital Control System (DCS).
Ultimately, we can provide a proposal with as little information as the batch size (tons/day or lbs/hr), inlet concentration and the desired diluted concentration. Each system can be customized to meet your layout, material preferences, and specific needs.
Turnkey System Includes:
Custom design to achieve your specified criteria ( dilution rate, concentration and temperature)
A quoted option includes a glycol chiller to use as cooling water. This will reduce operating costs significantly and reduce size of HX needed.
Conductivity sensors are located after the heat exchanger with flow control valves on acid feed will control product acid concentration.
Flow sensors on the acid feed will achieve consistent product and production rate
Level sensors and switches can be provided on tanks to prevent overfilling or running pumps dry
Flow sensor and switches are used on the cooling water to ensure safe and sufficient flow.
Temperature sensors on acid streams will ensure safe temperatures.
Instrument display, PID controllers, and pump controls are located for easy access.
Extracid – Dewatering System
The patented Extracid system uses a highly innovative approach to dewater sulphuric acid from low concentrations (10%) up to 97% at positive pressure. Vaporized water from the acid can be used as process steam and as such the Extracid process regains up to 70% of the system’s energy input. The system has a small footprint and saves on investment and operational costs.
This patented design, developed in conjunction with industry partner, Wilk-Graphite, was awarded the ACHEMA 2018 Innovation of the Year. The advancements it provides include:
- Elimination of vacuum system
- Safety and Reliability with a lifetime guarantee against corrosion
- Significant energy savings with heat recovery
- High purity product
Most sulfuric acid dewatering systems operate under vacuum due to insufficient material options. Extracid’s specialized SiC (silicon carbide) ceramic components, capable of operating at 500C+ and inert to all concentrations of sulfuric acid, provide the design freedom to safely and reliably operate at positive pressure.
Chiefly, the heart of the system is the Umax SiC block heat exchanger. The columns, compensators, and piping system are also unique designs constructed of SiC. The SiC materials of construction are proven universally corrosion resistant throughout the range of concentrations the system will see. This includes any HF that might be part of the water acid stream.
Benefits at a glance
- Constant product concentration even at the variable inlet
- Produces process steam as a useable product
- Up to 70% energy recovery
- Low investment and operation cost
- No corrosion
- Skip mounted
- Smaller equipment envelope (footprint)
- Resistant at HF and other components
- No abrasion
- Low fouling
- Decomposes organics
- High purity product
Regeneration
Regeneration of the spent Sulfuric Acid is equally important in many cases for economic and environmental reasons.
Commonly supplied at 93% concentration but diluted as a reactant or for its end purpose, its corrosivity and material compatibility will vary greatly with concentration and temperature. Although Impervite graphite is a suitable choice in many instances, the Umax Advanced Ceramic heat exchanger is becoming the design of choice.
There are two choices for handling the spent acid – either neutralize the spent acid and dispose of it or, regenerate it to remove the impurities so the acid can be reused. With the current high demand, sulfuric acid regeneration is quickly becoming the preferred method for both economic and environmental reasons.
Common Processes that Require the Regeneration of Sulfuric Acid:
- The alkylation process, H2SO4 catalyst is used to react isobutane with a light olefin to produce the alkylate component used in high octane gasoline.
- The viscose-rayon process uses H2SO4 spin baths in the production of rayon fibers and cellulose films.
- NOTE: Impervite PPS-GR works well in this application featuring industry-leading serviceability and material compatibility
- Because of its affinity for water, a common use of H2SO4 is as a drying agent.
Material and Design Considerations:
For heat transfer applications involving sulfuric acid, materials of construction vary depending on the temperature, concentration, impurities, required service life and cost effectiveness. Common cost-effective materials include SiC ceramic, graphite, and polyphenylene sulfide (PPS-GR).
Because of its resistance to corrosion in H2SO4 at all concentrations and most temperatures incurred in regeneration processes, PTFE lined steel is a commonly used for the construction of towers, separation drums, and other vessels utilized in regeneration, especially in positive pressure systems. PTFE can be rotolined for use under vacuum.
Also, several of sulfuric acid’s thermal properties require particular attention when considering heat and mass transfer systems involved in regeneration.
The viscosity of sulfuric acid varies significantly with temperature and concentration. With increased concentration and a decrease in temperature, viscosity will rapidly increase.
Additionally, vacuum conditions are frequently required when reconcentrating sulfuric acid because it has a low vapor pressure. At lower concentrations, the vapor pressure is mostly governed by the water. However, at higher concentrations, the degree of vacuum will have a more significant effect on the process temperature, which will in turn affect the energy input for the separation. This could result in higher process temperatures, reduced efficiency, and limited material options.
Electrical conductivity varies with concentration as a parabolic function, resulting in two concentrations described by the same value. Further, this condition needs to be considered in choosing measurement and control devices. Several approaches can be taken depending on the precision required.
Learn more by downloading this white paper, Important Considerations in the Regeneration of Sulfuric Acid, or watch CG Thermal’s presentation from CRU-Sulphur + Sulphuric Acid 2021.
Please provide us with your requirements. We look forward to using our expertise to assist you.
Technical Documentation